Company visit - IKEA Warehouse
- kkwlam2
- 2016年2月25日
- 讀畢需時 7 分鐘

Company background and development
IKEA was found in Sweden in 1943 by Ingvar Kamprad who grew up in Elmtaryd, Agunnaryd. It sold small items initially, then affordable and quality furniture to mass-market consumers through mail-order catalog. In 1953, it introduced the unassembled flat packaging to help minimize transportation costs and prices and transfer assembly costs to customers. After the introduction, most of the IKEA furniture was designed and sold in that unique method. By 1974, IKEA had grown from 1 showroom to more than a dozen stores in Europe. It continued to grow while entered Russia in 2000 and had built a network of 14 stores there. From 2005, the company started to enter Asia, beginning from Japan, and designed new products that suit local tastes. By 2013, there were already 16 stores in China which generated a total sales of €740 million while the Group also expanded their markets to India at the same period.
Currently, IKEA owns and operates 303 stores and franchised 42 stores from Inter IKEA Systems B.V. It has become the world leader of its main market of home furnishing and faced no comparable global competitor. The company has also been emphasizing sustainability through implementing the “People & Planet Positive” sustainability strategy from 2012.
Warehouse in Kwai Chung

Our visit


Products are packed in flat packages while some of them make up with 2 different packs of component.

A place where enable all the material handling equipments, such as the reach trucks, counter balance trucks and the pallet stackers to be charged for further uses.

Some products with loose pack picking offer to the retail stores in react with different demand.

Different products are ready for transporting, while staff is required to pick and build up those products on a pallet in a way that is safe and easy for transporting.

Flat packaging is well-known from IKEA that can help optimise loads and minimize transportation cost.
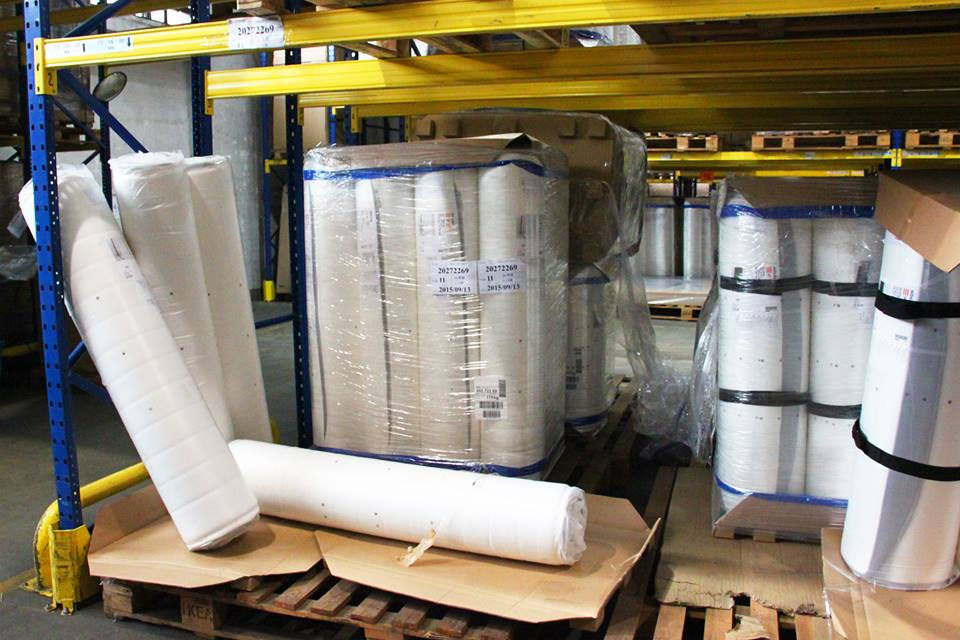
Despite flat packaging, IKEA has also started to use the method of rolling so as to minimize transportation cost.
Q & A
1. How do you do the demand forecasting and manage the supply in order to have a stable supply and prevent stock out?
IKEA will use the historical data as a base to perform demand forecasting, for example, using the performance report of past few weeks to project the demand. Also, IKEA make use of the LT3.3, which help control lead time tightly, to make sure of a stable supply, hence, the deviation between orders taken and products received is small. This is subject to sales as if the sales volume is much larger than IKEA’s forecast, stock out will still occur. Yet, unless the stock out situation is so sudden, IKEA can still manage it by shifting inventory from other distribution centers such as Shanghai to Hong Kong within only 19 days.
2. As most of your customer order deliveries are outsource, how would you ensure their quality of service, such as on time delivery, customers services?
IKEA emphasizes on on-time delivery to customer, therefore it is crucial to hire contractors with good quality service. To monitor the contractors, IKEA uses its Key Performance Indicator(KPI) system which evaluate the services provided from the contractors in three main criterias: on-time delivery, customer complaints, replacement orders. There will be a certain percentage of reward if contractors met the target performance set, but if their performances were below standard, penalties will then be given.
Besides, IKEA is also currently reviewing the policy and practice of whether to outsource the service of home delivery. Since it is difficult to control the performances of contractors, IKEA is considering weather to conduct all deliveries by itself or outsource some and conduct by itself partially.
3. What are the reasons behind IKEA to add the catering service at each store?
IKEA wants to bring a comprehensive experience to customers who are expected to spend a whole day with their families in the stores. It has considerably thought of providing catering services after the families have been measuring and choosing the furniture that they might buy, so they can have their meals and have a place to discuss on buying which type of furniture at the same time. Then, they could continue shopping for the others small items and take the pieces of furniture that are in flat package if needed at the end of their “IKEA tour”. At last, customers could also consider having a cup of tea and snacks after paying at the cashier. This service increase customers’ staying time in IKEA.
4. What are the competitive advantages of IKEA Hong Kong over your local competitors like Pricerite in terms of warehouse management?
Inventory management of IKEA helps it to differentiate from the market. Having customers select the furniture and retrieve the packages themselves is an inventory management tactic called ‘cost-per-touch’. Most IKEA furniture is designed and sold in pieces of flat packages for the customer to assemble. This unique packaging takes up less space in warehouse and transportation tools, which allows more spaces to stock additional items. Therefore, IKEA saves up stocking and transportation costs so as to focus more capital on core business.
Besides, IKEA used POS(point-of-sale) data and warehouse management system data. All these can help to generate how much quantity of each items need to order and sold. From these data, they can forecast sales for the next couple of days and order in the suitable amount of products to meet that demand.
Furthermore, while competitors may owns their distribution centers in China, IKEA owns its 32,000 square meters distribution center, where whole standardize stocks are kept, in Hong Kong. Hence, IKEA can have shorter lead time to response on demand of their retail stores in Hong Kong.
5. What are the current practices in your warehouse related to the company’s sustainability strategy?
IKEA’s return and replacement policy guarantees customer could return or replace their qualifying goods or furniture that may be in defect within 30 days after payment. Those products received will then be transported and gathered in the warehouse and put through a screening process of determining the product’s degree of defect. If the defects are small, products may be repaired for resell or saved up to be spare parts, otherwise, they may be recycled or donated to charities. Those products would be disposed only when they are in a very bad conditions.
6. At your distribution center, what are the meaning of the high flow and low flow in the supply chain?
Low flow also called slow moving goods, which refers to inventories that have lower turnover rate, and are less demanded by the customers. IKEA has to keep those stock longer than high flow inventory before sales.
High flow refers to inventories that have higher turnover rate, and are more demanded by the customers. High flow products will have more frequent stock replenishment and require larger batches. Cups are one example of high flow products.
7. Which part of operations in the warehouse is the most costly? How do you reduce the operational cost without affecting the efficiency?
IKEA has been hiring contractors to conduct daily unload operations. However, this part of operation is costly, so IKEA unload the cargo by themselves in non-peak season when there are only small amount of goods in order to save cost. At the same time, this practice can also maintain the unloading skill of staffs so as to raise their competitiveness. As long as there are contractors terminating the contract immediately, IKEA staffs can still be able to continue the operations and delivery services efficiently and effectively.
8. As we all know that the rental price in Hong Kong is high, how do you maintain low inventory level?
To counteract the skyrocketing rental, which doubled when compared with last year, IKEA has a couple of approaches to tackling this challenge. Besides the first one, a conventional approach, that is to minimize the incoming stock need, IKEA of Hong Kong branch intends to make the best use of vendor house stock approach - which is mainly applied to sofa inventory-- in which a third-party direct delivery (DD) stock in Shenzhen with short transportation time length cooperates with IKEA in Hong Kong, temporarily holding a required level of inventory owned by IKEA Hong Kong, mainly unassembled products or inventory taking up much storage capacity, such as sofas, and continually delivering a designated amount of inventory to IKEA warehouse in Kwai Chung under a time schedule. By doing so, the mounting burden of storage capacity in IKEA’s Kwai Chung warehouse is significantly released. Additionally, Kwai Chung warehouse of IKEA is able to spare 1500CBM storage space for other uses.
What is more, secondly, IKEA in Hong Kong has recently outsourced low-price warehouses in Shenzhen which, Simon mentioned, is served as a storage place holding all incoming inventory from abroad before forwarding them to Hong Kong. IKEA, as a result, not only can keep the inventory level of Kwai Chung warehouse low, but also enjoy the low-cost (approximately half the rental in Hong Kong) spacious warehouse neighboring Kwai Chung warehouse. “It is estimated that we can achieve breakeven if the inventory is at first stored in warehouse in Shenzhen for at least 30 days and then transferred to Hong Kong when requested.” said Simon.
9. How do you trace and track the product items during the inbound logistics and the outbound logistics?
During the operations of inbound logistics, IKEA traces and tracks(T&T) its products by communicating frequently among different parties in their supply chain in order to exchange information. For example, shipping company will update the shipment information to IKEA regarding the time of the ship arriving in Hong Kong.
During the operations of outbound logistics, IKEA operates its own T&T system for home delivery service. It can trace where the products are being transported.
10. IKEA is producing products which can be recycled and reused, does IKEA collect back these products from the customers? If yes, how does the reverse logistics of IKEA work?
Yes, IKEA does collect back all products when customers make request of repair or return. Yet, whether the returned products are recycled or reused is subject to the degree to which that product is worn-out. Returned products are either recycled as spare parts for alternative uses or disposed.
After receiving call for returning products from customers, IKEA will send staff to collect and transport the product back to the warehouse to do inspection. The staff will try their best to conduct recovery or recycling so as to maintain the disposal rate as minimum level in order to align with the goal of IKEA Group - going for sustainable world.
Reflection
Comparing with the Cathay Pacific Cargo Terminal(CPCT), we had a chance to look into how products are being packed and stored in the racking systems. Products usually could be picked in forms of local M-pack, M-pack, loose pack, half pallet or full pallet. Though the entire process from the inbound to outbound logistics is not as automated as CPCT, IKEA warehouse still owns their marterial handling equipments, such as the reach trucks, counter balance trucks and pallet stackers, to increase their transporting efficiency. This three types of truck and stacker help IKEA warehouse to adapt to different packing and storing sizes of products so as to fit in to different retail stores' demand.
留言